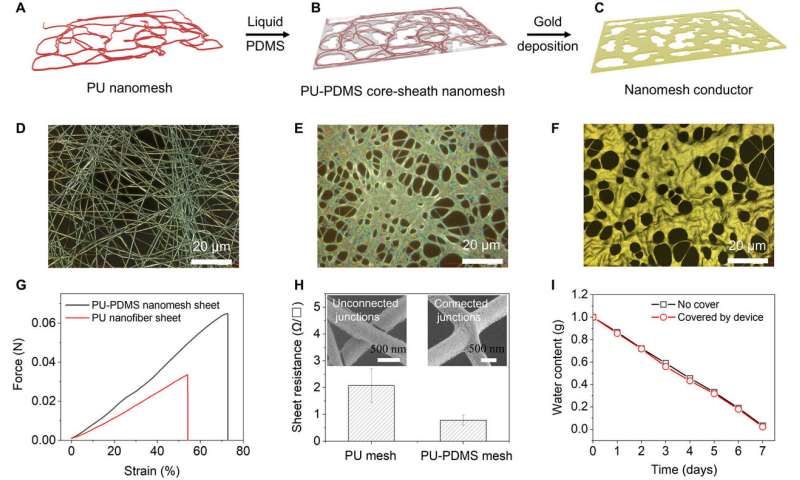
Comfortable strain gages can be directly placed on human skin to monitor continuous motion activity with widespread applications in robotics, human motion detection, and personal health care. However, it is challenging to develop an on-skin strain gage to monitor long-term human body motions without disturbing the natural movement of skin. In a new report now on Science Advances, Yan Wang, and a team of scientists in electrical engineering at the University of Tokyo and the Center for Emergent Matter Science in Japan presented an ultrathin and durable nanomesh strain gage. The device allowed continuous motion activity to minimize the mechanical constraints on natural skin motion. They engineered the device using reinforced polyurethane-polydimethylsiloxane (PU-PDMS) nanomeshes for excellent sustainability and durability. The geometry and softness of the device provided minimal mechanical interference for natural skin deformations. During speech tests, for instance, the nanomesh-attached face showed skin strain mapping similar to natural skin without nanomeshes. Wang et al. demonstrated long-term facial mapping to detect real-time, stable body movements with surface-bound nanomesh sensors.
Engineering a nanomesh
Wearable electronics for on-skin applications are designed to be thin, soft and durable to integrate with human skin for continuous long-term applications. Strain gages have attracted significant interest in bioengineering due to their applications in human-machine interfaces for health diagnostics. Soft and high-precision strain gages can be applied to continuously measure biological organ function. However, they have simpler mechanisms to generate repetitive electrical changes after mechanical deformation, for applications interfacing biological systems. The devices only require high mechanical compliance, flexibility, sensitivity and biocompatibility for optimal function. In this work, Wang et al. developed an ultrathin and durable nanomesh strain gage to detect human movement while minimizing mechanical constraints on natural skin. They used PU-PDMS (polyurethane-polydimethylsiloxane) to engineer the nanomeshes with an ultralight weight of 0.12 mg/cm2 and extraordinary mechanical durability for high-cycle stretching and releasing applications. The team used the setup to successfully map facial skin-strain during speech for up to 3.5 hours with minimal mechanical interference after long-term wear.
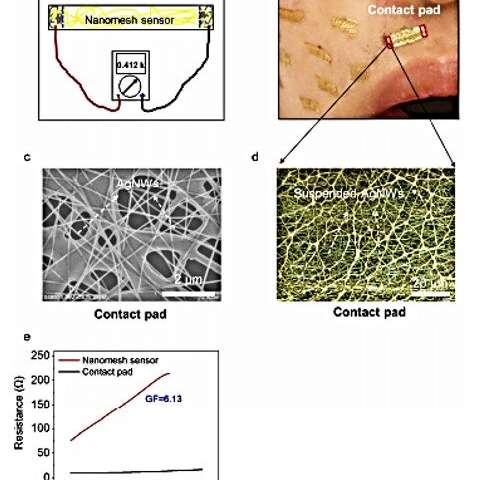
Development and characterization of nanomeshes
During the experiments, the team first electrospun PU (polyurethane) nanofibers to create long, hair-like fibers to form the backbone of the permeable nanomesh sensor. In the next step, they dipped the PU nanofiber sheet into a diluted PDMS (polydimethylsiloxane) solution for the nanofibers to form random bundles encircled by PDMS. Wang et al. subjected the material to mild ultraviolet (UV) ozone exposure to cure the surface and facilitate surface hydrophilicity (water-loving nature) for biocompatibility. They completed the device using gold deposition on both sides and observed the resulting PU-PDMS core sheath using scanning electron microscopy (SEM). The PDMS coating enhanced the interconnectivity between the nanofibers for improved structural integrity of the constructs. The resulting mechanical strength of the free-standing PU-PDMS nanomesh improved greatly with larger stretchability compared to the bare nanofiber sheet and the team also examined its gas permeability.
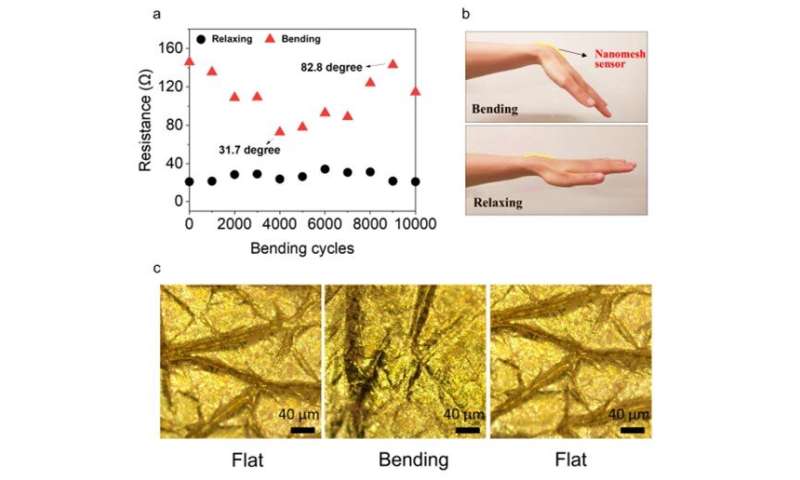
Programmable stretchability and sensitivity
Wang et al. effectively designed diverse nanomesh structures by varying the PDMS concentration to obtain nanomesh strain gages with different sensitivities and stretchabilities. However, all devices maintained similar pore size distributions relative to their porous structure. The scientists defined the gage factor (GF) or strain sensitivity as the ratio of fractional change in electrical resistance to the fractional change in length. Different mesh structures showed different stretchabilities and gage factors. During uniaxial stretching, the resistance of each device increased with different rates. By diluting the PDMS solution, they effectively programmed the nanomesh strain gages with different stretchabilities and sensitivities. At higher strains beyond the range of tolerance, the PU-PDMS meshes disconnected to cause nanomesh breakdown, while the nanomesh structure could be retained by releasing the strain.
Electromechanical sustainability, reliability and durability of PU-PDMS nanomesh sensors
To understand device sustainability, the research team applied a 40% strain on the device for 12 hours. They then performed cyclic tests to investigate the mechanical durability of the construct and noted a slight hysteresis in resistance in the first few hundreds of cycles due to the mechanical properties of PDMS. The sheet resistance of the PU-PDMS nanomesh was stable under 100 days of storage in ambient conditions due to its inert gold surface, indicating a long shelf life, well-suited for practical applications. The scientists conducted durability tests for the nanomesh sensors using constructs engineered with diverse nanofiber scaffolds including polyvinyl alcohol (PVA), polyurethane (PU) alone and PU with parylene coating. Compared to the three other nanomeshes that did not perform so effectively, the PU-PDMS nanomeshes showed uniform cyclic strain during 100 cycles.
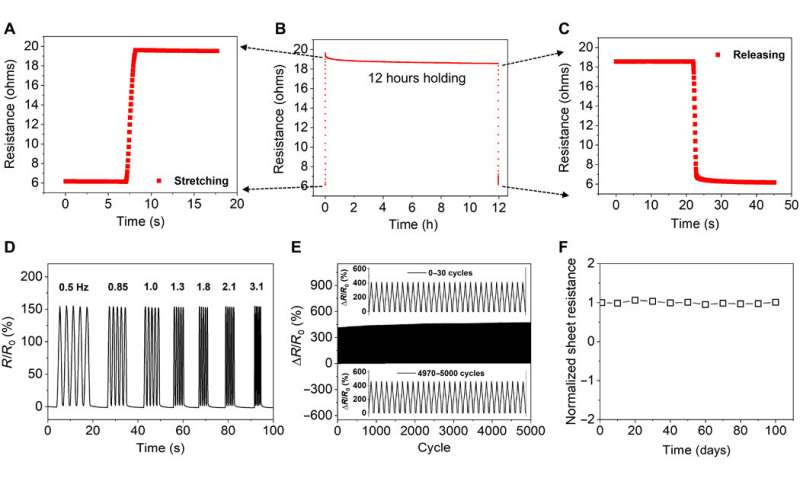
Proof-of-concept on-skin strain gage
After attaching the nanomesh device to human skin, the team sprayed the surface with water mist for stable adherence. The contact was barely perceptible to the subject wearing the nanomesh sensors during the experiment. Wang et al. attached nanomesh sensors on the right side of the face and placed black rectangle markers on the left side as a reference. When the test subject articulated the letters “a,” “o” and “u,” the highest strains recorded for black markers ranged between 17.5 to 25%, while those recorded for nanomesh sensors were 18.3 to 23.6%. The strain mapping results therefore showed symmetrical skin strain distribution on the right and left side of the face, highlighting minimal mechanical constraints of nanoscale devices on the skin during speech. The conformable nanomeshes could be worn for 3.5 hours without discomfort.
The team then extended the experiments to detect subtle skin deformations on the human wrist induced by pulse. They gently pressed the radial artery of the human wrist attached with a nanomesh sensor and picked the amplitude and frequency in real time, the device can be used to monitor signals before and after physical exercise. The construct maintained higher linear stretchability to detect large joint bending motions with excellent compliance to prevent breakage or detachment from the skin. The strain sensor maintained effective functionality even after 10,000 bending/relaxing cycles to demonstrate its structural integrity and conformability between the skin and the device.
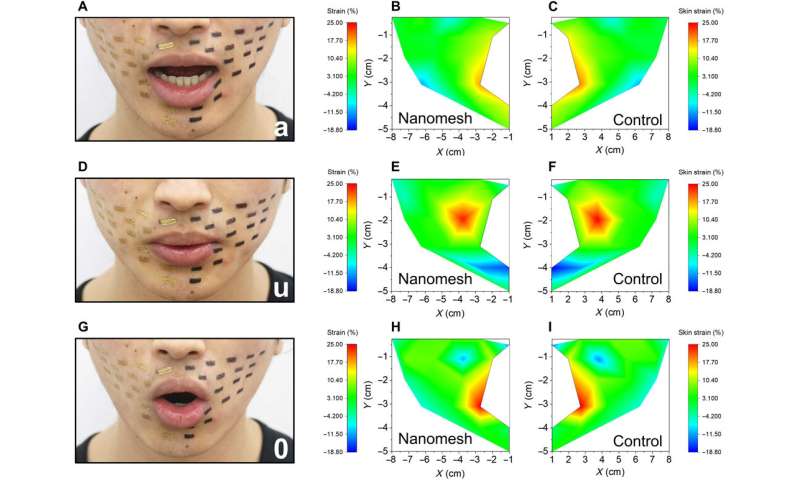
In this way, the PU-PDMS (polyurethane-polydimethylsiloxane) based ultra-soft, multi-layered nanomeshes developed in this work were thinner and more stretchable compared to preceding work conducted by the same team. The constructs displayed remarkable durability and sustainability during cyclic stretching tests. The mechanical durability was a key feature for long-term high-precision skin monitoring tests in real time. The nanomesh sensors are well suited for a range of practical applications including remote personal health monitoring, tracking endurance sport performance and as skin-machine interface prosthetics. Wang et al. suggest replacing the gold surface coat with more cost-effective conductive nanomaterials to construct nanomesh electronics in the future. The scientists envision these constructs will become applicable as futuristic on-skin/implantable electronics for everyday healthcare monitoring activities.
Yan Wang et al. A durable nanomesh on-skin strain gage for natural skin motion monitoring with minimum mechanical constraints, Science Advances (2020). DOI: 10.1126/sciadv.abb7043
Sunghoon Lee et al. Ultrasoft electronics to monitor dynamically pulsing cardiomyocytes, Nature Nanotechnology (2018). DOI: 10.1038/s41565-018-0331-8
Takao Someya et al. Toward a new generation of smart skins, Nature Biotechnology (2019). DOI: 10.1038/s41587-019-0079-1
Science Advances
,
Nature Biotechnology
,
Nature Nanotechnology